AFCON CUSTOMER PROFILE
Alvin Brown
Alvin, owner and manager director of Thermal Dynamics & Engineering and JNC Thermal Systems, has been working in the HVAC&R for 20 years. He has gained much experience allowing him to specialise in chillers, so we sat down with him to discuss how he began his career, where it has taken him and what he feels helped him get where he is today.
What is your general background?
Why did you go into this industry originally? My father was the Refrigeration & Air-Conditioning Engineer at Beacon Sweets for 23 years, this naturally drew my interest to the trade from my young high school days. He started teaching me to repair small scale refrigeration equipment in our garage from the time I was in grade 10. After matriculating, I did my apprenticeship at York International, qualified, then slowly moved my way up in the Industry, ultimately to opening Thermal Dynamics & Engineering in 2009.
Where did you study or do your apprenticeship?
I studied at UNISA, did my apprenticeship, and many plant specific training courses, at York International.
Where have you worked over the years?
Started off at Million Air Services(about 2 years), spent 4 years at York International, spent a short 7 months at Combined Air Services, spent 6 years as a service manager and share holder at DJ Thermal Engineering, opened Thermal Dynamics & Engineering beginning of 2009 until present.
Where did you gain your chiller experience?
Fortunately, I was well trained on chillers from York International days, grew and gained experience throughout my career, actually still learning now, you never stop learning.
How long have you been working in the industry and how long specifically with chillers?
Been in the industry for 20 years and have been exposed to chillers since the beginning.
What do you enjoy about working with chillers, which led to your specialisation in them?
I like to specialize in a field, you tend to always be needed in the industry.
What plants have you worked at in the past? Or do so currently?
Eskom Power Station in Drakensburg, Boxmore Plastics (Harrismith, CPT, Bloemfontein & Mauritius, Zambia), Coca Cola (PE, Mozambique & Mauritius), St Augustines Hospital, Sasko Bakery, Boxer Meats Factory in Ballito, just to name a few. All the plants at the above sites are chillers for production purposes. We also work on several cold storage facility plants which run on screw compressors (low temperature and medium temperature), a few ammonia screw sets used for food production blast freezers and many air-conditioning systems from chilled water to standard DX split systems.
Which fouling factors does Onda suggest for the selection of shell and tube heat exchangers?s?
The fouling factor is important for the selection of an evaporator. The value Onda suggest to input in selection software are:
For evaporators: - Normal water in closed circuit: 0,000043 m2K/W; -
Water in open circuit: 0,000086 m2K/W; -
Solutions with glycol <40%: 0,000086 m2K/W; -
Solutions with glycol >40%: 0,000172 m2K/W.
For condensers: -
Normal city water: 0,000043 m2K/W; -
Treated tower water: 0,000043 m2K/W; -
River water: 0,000086 m2K/W; -
Solutions with glycol <40%: 0,000086 m2K/W; -
Solutions with glycol >40%: 0,000172 m2K/W.
Contact our heat exchanger department - Afcool Heat Exchangers
SAIRRAC Golf Day
The SAIRRAC Golf Day took place on Friday the 2nd of September, where Afcon had both a 4 ball participating as well as sponsoring the 11th hole.
Tarryn Ching did a fantastic job of organising and ensuring that the day was a success, and as always the HVAC&R industry support was outstanding. The supplier support was excellent, with multiple suppliers sponsoring holes, which added to the festive atmosphere. As well as lots of suppliers and contractors participating in the golf day. All golfers, pro or amateur, could be seen enjoying the day, lots of fun was had and many beers drunk.
Is it always lovely for industry members to get together, share camaraderie and swop war stories.
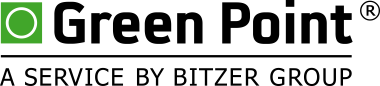
Afcon has sent compressors to Bitzer Green Point Johannesburg to be assessed, quoted on and subsequently overhauled with great success. The over all experience has left us very pleased with the availability of this service, and we look forward to utilising it in the future.
Bitzer’s “Green Point” Program was set up in Johannesburg in 2015. The program is part of a global network of service centres, which boasts a reliable service and overhaul for your reciprocating and screw compressors. The technicians have been trained at the Bitzer Green Point international training centre in France and receive constant support from Bitzer as well as are updated with its latest developments. Green Point employees maintain, overhaul and repair BITZER compressors.
Dave Nicholl’s was recently involved in an interesting installation involving CO2 at a large retail store in KZN and here’s what he had to say about it...
AFCON Industrial Equipment are Bitzer agents in KwaZulu Natal. We hold a large range of stock in spare parts at our office in Durban & can identify parts that you may need.
AFCON has been Bitzer agents since 1999 and have a wealth of experience in Bitzer products.

Refrigeration - Disposable Packaging:
Refrigerant Branding
Refrigeration Product Batch Number
used as a reference between the disposable cylinder and the Certificate of Analysis. This batch number also appears on our box.
Refrigeration - D.O.T. 39
Refrigeration Manufacturing Codes and Disposable Batch Number
Refrigeration Safety Data Sheet (SDS)
Refrigeration - Certificate of Analysis (COA)
Fundamental terms
On an international level, the use of the Systeme International d’Unités is used in refrigeration. This is often referred to as the SI-system. For a number of countries the implementation of the SI-system is still an on-going process. However, in many parts of the refrigeration community metric units or other alternative units are still used (the practically used alternative units will be shown in brackets). The table shows the SI-units and the other often used alternative units.
Temperature
Temperature is a very important part of refrigeration. Almost all refrigeration systems are for the purpose of reducing the temperature of an object like the air in a room or the objects stored in that room. The SI-unit for temperature Kelvin [K] is an absolute temperature because its reference point [0 K] is the lowest temperature that it in theory would be able to obtain.
When working with refrigeration systems the temperature unit degree Celsius [°C] is a more practical unit to use. Celsius is not an absolute temperature scale because its reference point (0 °C) is defined by the freezing point of water (equal to 273.15 K). The only difference between Kelvin and Celsius is the difference in reference point. This means that a temperature difference of 1 °C is exactly the same as a temperature difference of 1 K. In the scientific part of the refrigeration community temperature differences are often described using [K] instead of [°C]. This practice eliminates the possible mix-up of temperatures and temperature differences.
Refrigeration - an introduction to the basics
Refrigeration is a process that removes heat. A refrigeration plant is used to cool down articles or substances, and maintain them at a temperature lower than the ambient temperature.
At the beginning of the last century, it was discovered that the growth of micro-organisms relies on temperature, growth declines as temperature falls, and after +10°C growth slows considerably. This knowledge allowed the use of refrigeration to conserve foodstuffs using natural ice. The first mechanical refrigerators for the production of ice appeared around the year 1860. In 1880 the first ammonia compressors and insulated cold stores were put into use in the USA. Electricity was used from the beginning the 20th century and mechanical refrigeration plants came into being. After the Second World War small hermetic refrigeration compressors were produced refrigerators and freezers began to be used in the home. Today, these appliances are regarded as normal household necessities.
Durban, 24 June 2015
I recently discovered this article on the internet originally written in 2008. In 2008 the Bitzer Open Drive Compressors as well as the Marine Condensors used for the air conditioning plants on the Tugs were supplied by Afcon Industrial Equipment to the contractor. This was seven years ago and I am pleased to report that the shipbuilding industry is still thriving in Durban and has been awarded the contract for a further eight tugs to be built. At Afcon we pride ourselves on keeping all details of orders supplied. We have again supplied the Compressors and Condensors and the Racks are currently being manufactured off site by our customer for fitting onto the Tugs when ready. (http://www.fad.co.za/Resources/sa-ships/default.htm).
Huge boost for shipbuilding in Durban
By Allan Jackson - October 2008
An order for five harbour tugs valued at over R400-million is currently under construction for the Transnet National Ports Authority. This has made the future for shipbuilding in Durban look brighter than it has for many years.
This is according to Louis Gontier, MD of Southern African Shipyards.. The firm, located at Bayhead in the city, is currently hard at work building the first five tugs in tandem, and expects to launch the first in July 2009 and complete it in October 2009. Gontier said that he was proud to receive the order from the NPA as this showed that the firm had earned the approval of the TNPA.
The TNPA has called for tenders for the building of eight additional tugs and adjudication is imminent. SAS are confident that they will secure at least part of this order, and possibly the entire order.
The five tugs, or water tractors as they are sometimes also known, will be built to a design by Naval Africa, around principles laid down by Voith Schneider, whose propulsion systems will be installed in each of the vessels. Instead of normal screw propellers, the Voith system uses two counter-rotating discs, each fitted with 5 symetrical blades, mounted vertically.
The system, which was invented over 100 years ago, gives vessels the ability to sail in any direction and turn on their own axis, ensuring the highest levels of maneuvrability and safety. Each tug will be equipped with two MAN engines giving a total of 5300KW of installed power, and will be able to perform a bollard-pull of 70 tons, making them the most powerful tugs in the TNPA's fleet.
The quality of workmanship on the tugs is equal to anything available in Europe due to extremely stringent quality checks carried out at all stages of the building. South African Shipyards is ISO 9001/2000 certified by TUV Rheinland. In addition, the TNPA has a technical representative permanently onsite to conduct checks and he is backed-up at all stages by an inspector from French standards organisation, Bureau Veritas.
Gontier says he still cannot really believe how rapidly South African Shipyards has taken off since it was bought by himself, another private investors and BEE partner Hlahlindlela Investments in January 2006. The company also allocated 12% share to its employees trust. Using finance obtained from the KwaZulu Natal Growth Fund, the investors obtained the prime Bayhead property, complete with buildings and equipment.
The NPA was about to order a number of tugs and the purchase was made with a view to winning the orders or, if that failed, of establishing a marine and ship repair park to attract tenants. In the event, a number of tenants did move in but it wasn't long before an order for three tugs was obtained and, six months later, an order for two more.
No ships had been built in Durban for a number of years but the company found that there were still a sizeable number of people available with the necessary skills. This includes Jurgen Cobarg, who became the company's shipbuilding general manager.
The construction of the first vessel started in August 2007 and others have followed at regular intervals since then. The vessels are being built in a 320m long and 30m high building on a production line large enough to beggar my imagination when I visited it. A second hall of some 300m long is being used to fabricate smaller components.
The company is not immune to skills shortage faced by industry as a whole, and recently embarked on an apprenticeship program. Regular intakes of apprentices are now being taken on for training in various disciplines including boiler-making, electrical, fitting, welding, mechanical, and rigging. It is generally accepted that each shipbuilding job has a downstream multiplier effect of eight. This means that around 2000 people are depending for their livelihoods on the vessels now being built at South African Shipyards.
Gontier is very optimistic about the future of his company, saying that enormous interest is already being shown by foreign owners in Durban-built vessels. He also said that the company had recently played host to Vice Admiral Mudimu, Chief of the South African Navy, and he said he was hopeful that the company would get involved in the building of inland and offshore patrol vessels for the navy.
The signs were also good, he said, that foreign organisations were becoming interested in the company's expertise in building Voith-pattern harbour tugs and that, after completing the five on order from the TNPA, the company would hopefully be in the running for international orders for the same type of tugs.
Also helping to secure the company's future and create even more jobs is their recent establishment of a ship repair division, which completes afloat and dry dock repairs and provides riding gangs which can perform repairs while vessels are on the move. Management are astonished at the growth in that side of the business, which started off from a zero-base in November 2007 and grew rapidly to the stage where turnover burst over the R12-million mark in July, just over six months later.
Regarding proposed plans to do with digging out the area at Bayhead, to build more container handling capacity for the port, Gontier said that, as far as he was concerned, the company had a lease on the land until 2022. He pointed out that it had been estimated that it would cost around R300-million to move South African Shipyards to another site, and provide it with the same facilities it currently has.
FRIGAIR South Africa
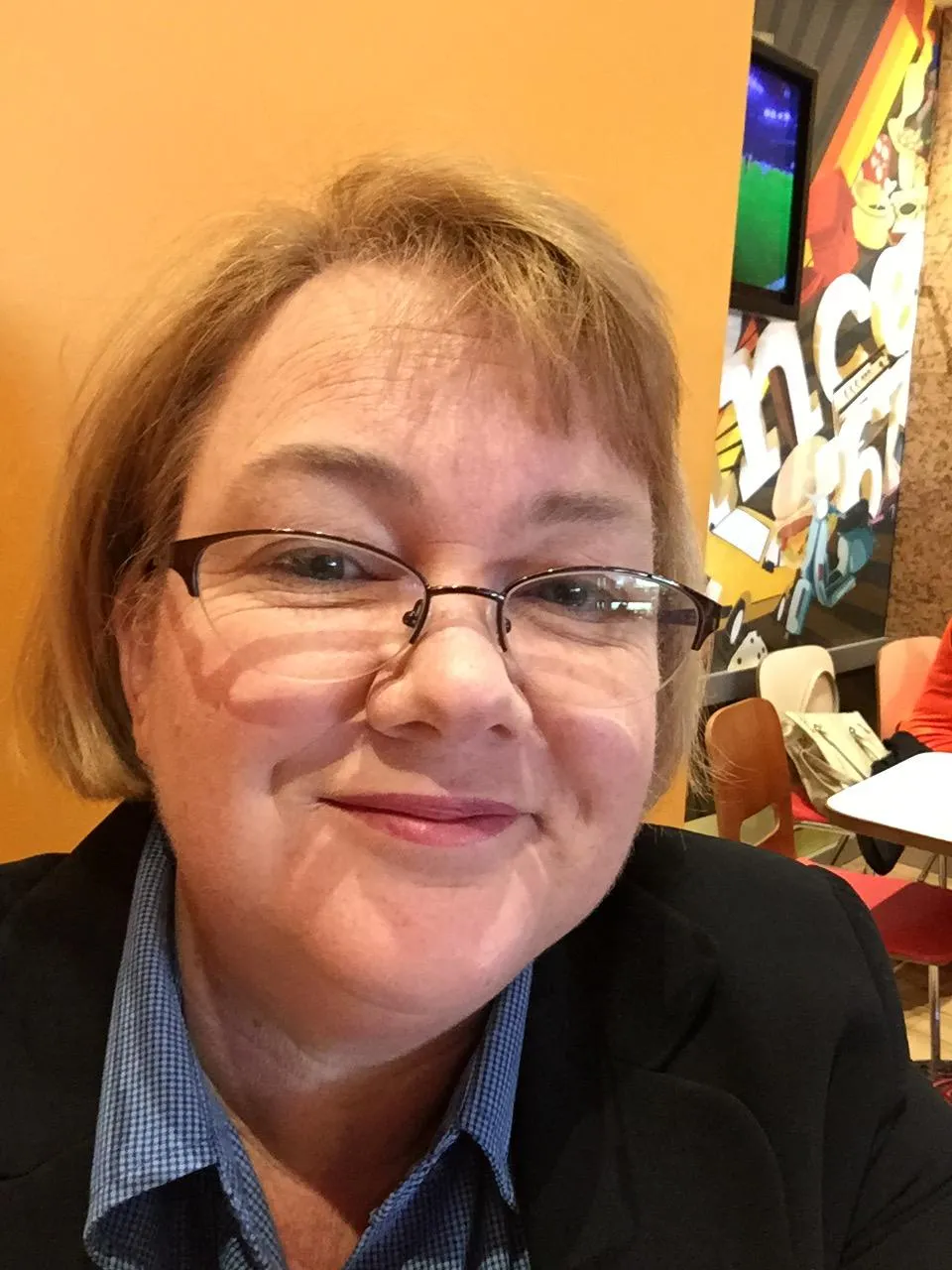
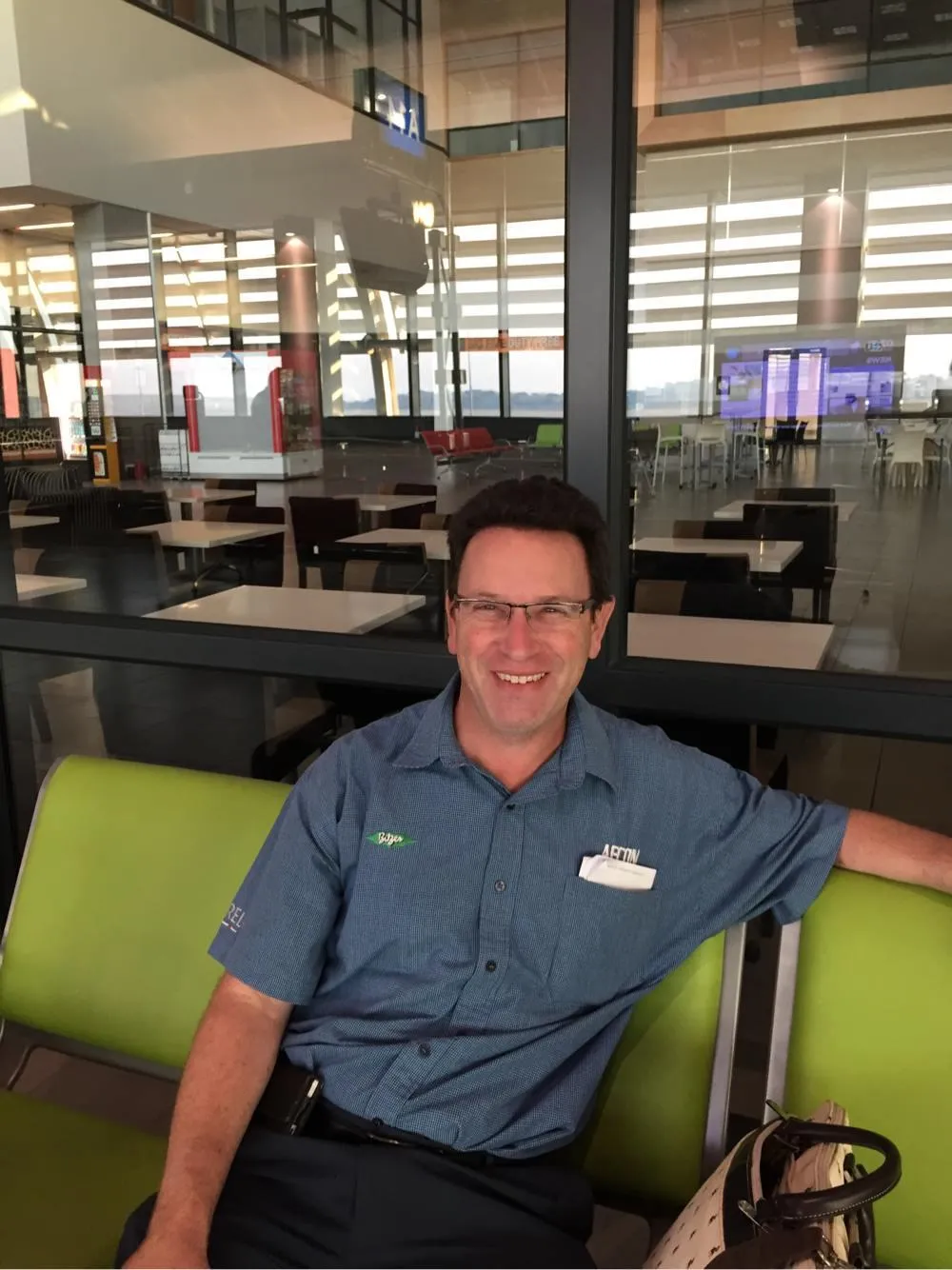
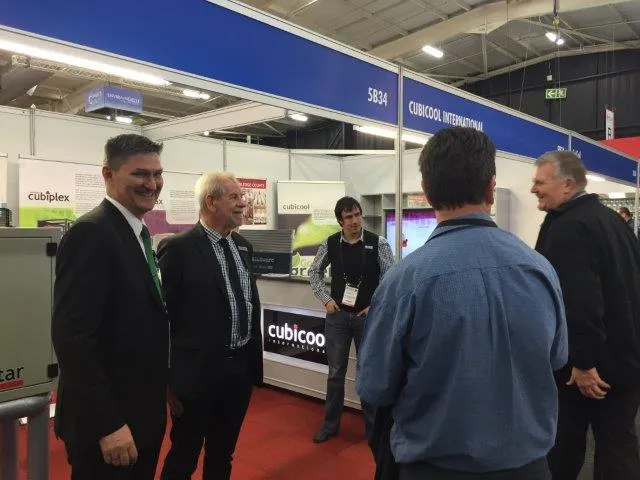
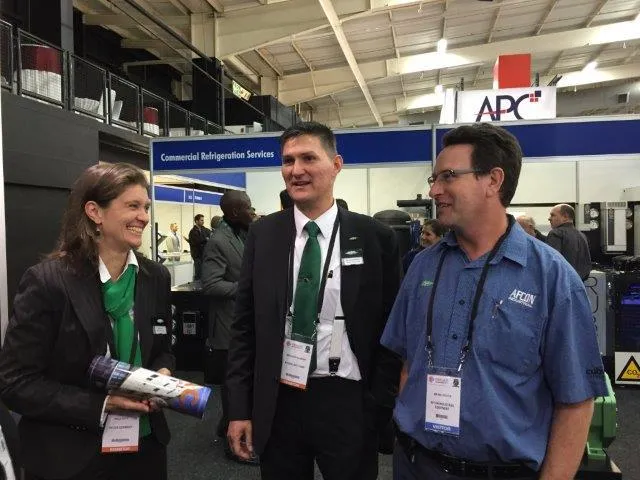
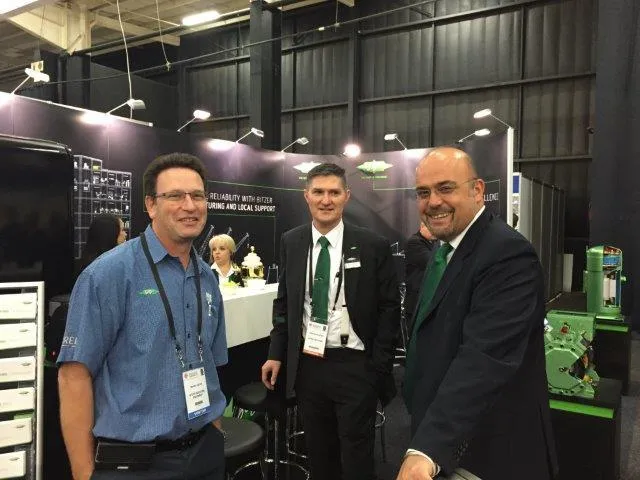
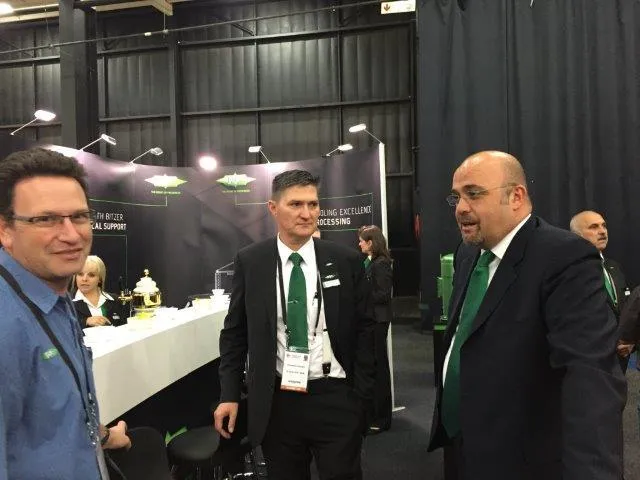
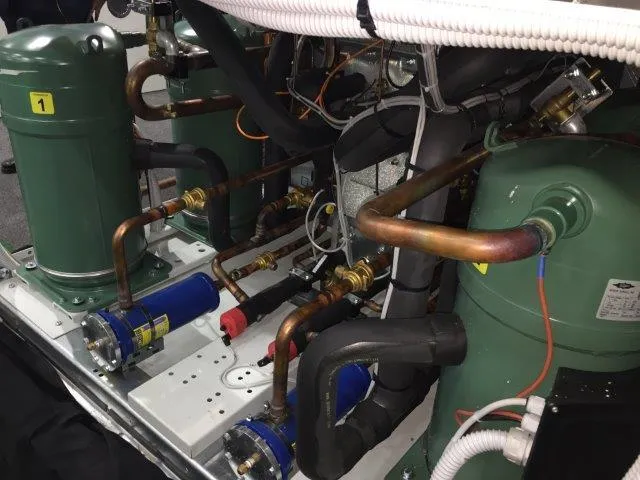